The Cost of Cutting Corners: Why Hiring a Qualified Industrial Electrician Isn’t Optional
In high-stakes environments like manufacturing plants, data centers, and processing facilities, your electrical systems aren’t just important—they’re mission-critical. So why do so many operations risk safety, downtime, and compliance by avoiding a specialized industrial electrician?
Whether it’s to save money, avoid short-term downtime, or simply out of habit, many facility managers choose to handle electrical needs with in-house staff or general electricians. But what looks like a smart cost-saving move on the surface can quickly spiral into something far more expensive.
At StandTech Electric, we’ve been called in to fix the aftermath of these decisions for over 20 years. From catastrophic machine failure to failed inspections and lost revenue, we’ve seen what happens when industrial electrical work is handled by someone who’s not trained for it.
Here’s what you risk when you don’t hire a qualified
industrial electrician—and what you gain when you do.
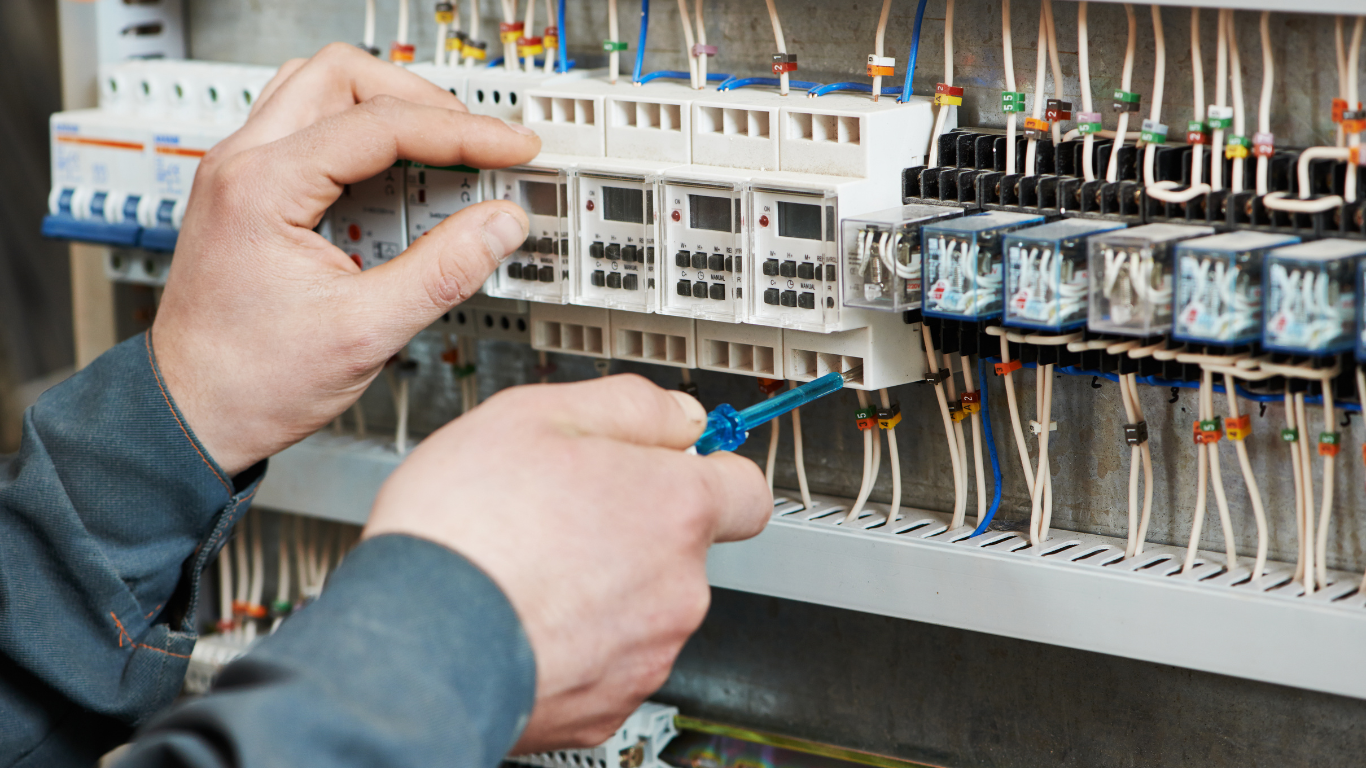
I. Why Industrial Electrical Work Is a Different World
Industrial electrical systems are vastly different from those in homes or small businesses. We're not talking about standard wall outlets or dimmer switches—this is high-capacity, high-voltage, high-liability work.
Industrial electricians are trained to handle:
- Complex automation systems like PLCs (programmable logic controllers)
- Motors, generators, conveyor systems, and control panels
- High-voltage distribution and power balancing
- Equipment-specific wiring for large-scale machinery
- Compliance with OSHA, NEC, and other industry-specific codes
Hiring someone without industrial-specific training isn't just a bad idea—it’s a direct risk to your people, equipment, and bottom line.
II. The Most Common Mistakes Businesses Make
When it comes to electrical systems, here are the mistakes we see most often at StandTech Electric—usually after something’s already gone wrong:
Mistake 1: Using a General Electrician for Industrial Work
General electricians are typically trained for homes or light commercial environments. Asking them to work on a production facility is like asking a family doctor to perform surgery.
Mistake 2: Relying on In-House Maintenance Staff
Your facilities crew might be great at many things—but unless they’re licensed for industrial electrical work, they should never touch control systems, high-voltage panels, or machinery wiring.
Mistake 3: Delaying Repairs Until There’s a Failure
Waiting until something breaks is a gamble. What seems minor—like a tripped breaker or an overheating motor—could be a warning sign of a systemic problem.
Mistake 4: Doing the Bare Minimum for Code Compliance
Passing inspection isn’t the same as having a safe, future-ready system. Minimal compliance often ignores efficiency, scalability, and risk mitigation.
III. The Hidden Costs of Unqualified Electrical Work
It might seem like you’re saving money by not hiring a specialist. But here’s the reality:
1. Equipment Damage
Improper wiring, grounding, or voltage handling can destroy sensitive equipment. Replacing a damaged CNC machine or power supply can cost tens of thousands—far more than any electrician invoice.
2. Downtime & Production Losses
When your line goes down, you're not just fixing a wire—you’re halting output. For some facilities, an hour of downtime can cost thousands in lost revenue. Unqualified work increases the risk of unplanned shutdowns.
3. Failed Inspections & Code Violations
Industrial environments are subject to strict regulations. If your facility fails an OSHA or NEC inspection, you could face hefty fines, delays in operations, or even full shutdowns.
4. Increased Insurance Risk
Insurance claims can be denied if electrical work was done by someone unlicensed or unqualified. That’s not a position you want to be in after a fire or electrical failure.
5. Fire & Safety Hazards
Improperly wired panels, overloaded circuits, or incorrect grounding can spark serious safety incidents. At StandTech Electric, we've seen businesses face evacuation, shutdowns, or permanent equipment loss due to something as simple as a miswired connection.
IV. Real-World Scenarios That Prove the Point
Case 1: DIY Fix Leads to Plant Shutdown
A food processing facility had a conveyor system acting up. Their internal team decided to “patch” the motor wiring. Two days later, the system failed completely—taking two production lines offline for three days. We were called in for emergency service, and it turned out a mismatched phase caused the failure. Total loss: 72 hours of production + $40,000 in repair costs.
Case 2: General Electrician Misses Code Issue
A distribution warehouse hired a commercial electrician to install new lighting and add a few circuits. They passed the initial inspection but failed their annual OSHA audit due to missing arc-flash labels and improper panel spacing—both industrial-specific code violations. Cost to fix: $12,000, not counting lost hours.
Case 3: Expansion Plan Fails Without Load Analysis
A manufacturing company added new CNC machines but didn’t evaluate panel capacity. The first week after installation, they began experiencing overloads and inconsistent power delivery. The machines were never calibrated correctly. StandTech Electric was brought in to upgrade the system—and recover the workflow.
V. What a Qualified Industrial Electrician Actually Provides
Hiring a true specialist like StandTech Electric comes with measurable value.
Here’s what our licensed industrial electricians bring to the table:
- ✅
Load Balancing & System Capacity Planning
We analyze your entire system and prevent overloads before they happen. - ✅
High-Voltage Equipment Installation
We handle transformers, switchgear, and panels that exceed standard capacities. - ✅
PLC Troubleshooting & Machine Integration
Automation is complex—we wire and program systems for seamless operation. - ✅
Safety Compliance & Audit Prep
From OSHA to NEC to local code, we ensure you pass inspections with no surprises. - ✅
Emergency Response 24/7
System down? We're available any time to restore operations fast. - ✅
Preventative Maintenance Programs
Routine servicing catches problems before they result in downtime or equipment damage.
This isn’t optional work. It’s the infrastructure that makes your facility safe, scalable, and profitable.
VI. Why You Actually Save More by Hiring an Industrial Electrician
Let’s flip the conversation: What’s the cost of doing it right the first time?
- No rework costs
- No shutdowns
- No failed inspections
- Lower long-term utility bills
- Fewer emergency repairs
- Better lifespan for all equipment
At StandTech Electric, our clients often find that our preventative strategies reduce service costs by 30–50% over three years compared to reactive maintenance.
VII. StandTech Electric: Your Trusted Partner in Industrial Power
For over 20 years, StandTech Electric has worked with Long Island’s most complex industrial environments, including:
- Manufacturing plants
- Pharmaceutical labs
- Water treatment facilities
- Food and beverage processing plants
- Steel and fabrication shops
- Warehousing and logistics centers
- Data and IT infrastructure hubs
We’re more than contractors—we’re partners in operational safety and efficiency.
Every StandTech technician is:
- Fully licensed and OSHA-certified
- Drug-tested and background checked
- Trained in industrial systems and safety
- Equipped with tools to diagnose and solve problems quickly
We’re locally based in Long Island and backed by the national support of Authority Brands, so you get both expertise and scale.
VIII. FAQs: Industrial Electrician Essentials
Isn’t a commercial electrician good enough?
No. Commercial electricians typically work on storefronts and office buildings—not facilities with PLCs, generators, or large-scale automation. Industrial electricians are trained for higher risk, higher capacity environments.
How often should I have my electrical system checked?
Quarterly maintenance is ideal, especially for older systems or those running 24/7. We offer customized plans based on your load and facility type.
Can’t my facilities team handle basic electrical fixes?
Even basic repairs in industrial systems involve high-voltage risks and strict codes. Unless they’re certified for industrial electrical work, it’s not worth the risk.
What if we already had a failure—can you help us get back online?
Absolutely. We offer 24/7 emergency industrial electrical services and specialize in fast diagnostics and recovery.
IX. Don’t Cut Corners—Cut Risk Instead
When you’re running a production facility, every hour of uptime counts. Trying to save a few dollars today by skipping a qualified industrial electrician can cost you thousands in downtime, equipment damage, or safety fines tomorrow.
At StandTech Electric, we help Long Island businesses operate safely, efficiently, and with confidence. Whether you're upgrading equipment, expanding operations, or just want to avoid the next failure, we’re the team to call.
📞 Reach us anytime at
(516) 407-3737
📩 Need an inspection or emergency response? Contact us today to schedule service
🛠️ Trust Long Island’s most experienced industrial electricians to keep your facility running right